Thermoplastic elastomer
Thermoplastic elastomers (TPE), sometimes referred to as thermoplastic rubbers, are a class of copolymers or a physical mix of polymers (usually a plastic and a rubber) which consist of materials with both thermoplastic and elastomeric properties. While most elastomers are thermosets, thermoplastics are in contrast relatively easy to use in manufacturing, for example, by injection molding. Thermoplastic elastomers show advantages typical of both rubbery materials and plastic materials. The benefit of using thermoplastic elastomers is the ability to stretch to moderate elongations and return to its near original shape creating a longer life and better physical range than other materials.[1] The principal difference between thermoset elastomers and thermoplastic elastomers is the type of cross-linking bond in their structures. In fact, crosslinking is a critical structural factor which imparts high elastic properties.
Types
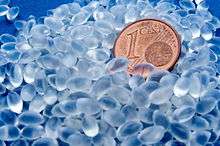
There are six generic classes of commercial TPEs:
- Styrenic block copolymers (TPE-s)
- Thermoplastic olefins (TPE-o)
- Elastomeric alloys (TPE-v or TPV)
- Thermoplastic polyurethanes (TPU)
- Thermoplastic copolyester
- Thermoplastic polyamides
Examples of TPE products that come from block copolymers group are THERMOLAST®, HIPEX®, COPEC®, and For Tec E® (KRAIBURG TPE), Santoprene (ExxonMobil), Termoton by Termopol Polimer, Arnitel (DSM), Solprene (Dynasol), Engage (Dow Chemical), Hytrel (Du Pont), Dryflex and Mediprene (ELASTO), Kraton (Kraton Polymers), Pibiflex. Example of TPV are THERMOLAST® A, THERMOLAST® V, HIPEX®, FORPRENE, and TERMOTON-V. Examples of Styrenic block copolymers (TPE-s) are THERMOLAST® K (SEBS),[2] THERMOLAST® M (SEBS), SOFPRENE (SBS) and LAPRENE (SEBS). An example of Thermoplastic polyurethanes (TPU) compound is COPEC® . An example of Thermoplastic olefins (TPO) compound is For-Tec E®. In order to qualify as a thermoplastic elastomer, a material must have these three essential characteristics:
- The ability to be stretched to moderate elongations and, upon the removal of stress, return to something close to its original shape
- Processable as a melt at elevated temperature
- Absence of significant creep
Background
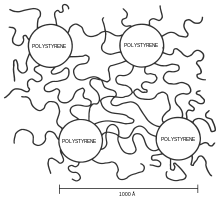
It was not until the 1950s, when thermoplastic polyurethane polymers became available, that TPE became a commercial reality. During the 1960s styrene block copolymer became available, and in the 1970s a wide range of TPEs came on the scene. The worldwide usage of TPEs (680,000 tons/year in 1990) is growing at about nine percent per year. The styrene-butadiene materials possess a two-phase microstructure due to incompatibility between the polystyrene and polybutadiene blocks, the former separating into spheres or rods depending on the exact composition. With low polystyrene content, the material is elastomeric with the properties of the polybutadiene predominating. Generally they offer a much wider range of properties than conventional cross-linked rubbers because the composition can vary to suit customer needs.

Block copolymers are interesting because they can "microphase separate" to form periodic nanostructures, as in the styrene-butadiene-styrene block copolymer shown at right. The polymer is known as Kraton and is used for shoe soles and adhesives. Owing to the microfine structure, the transmission electron microscope or TEM was needed to examine the structure. The butadiene matrix was stained with osmium tetroxide to provide contrast in the image. The material was made by living polymerization so that the blocks are almost monodisperse, so helping to create a very regular microstructure. The molecular weight of the polystyrene blocks in the main picture is 102,000; the inset picture has a molecular weight of 91,000, producing slightly smaller domains. The spacing between domains has been confirmed by small-angle X-ray scattering, a technique which gives information about microstructure. Since most polymers are incompatible with one another, forming a block polymer will usually result in phase separation, and the principle has been widely exploited since the introduction of the SBS block polymers, especially where one of the block is highly crystalline. One exception to the rule of incompatibility is the material Noryl, where polystyrene and polyphenylene oxide or PPO form a continuous blend with one another.
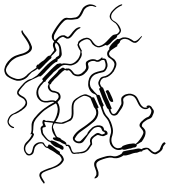
Other TPEs have crystalline domains where one kind of block co-crystallizes with other block in adjacent chains, such as in copolyester rubbers, achieving the same effect as in the SBS block polymers. Depending on the block length, the domains are generally more stable than the latter owing to the higher crystal melting point. That point determines the processing temperatures needed to shape the material, as well as the ultimate service use temperatures of the product. Such materials include Hytrel, a polyester-polyether copolymer and Pebax, a nylon or polyamide-polyether copolymer.
Advantages
TPE materials have the potential to be recyclable since they can be molded, extruded and reused like plastics, but they have typical elastic properties of rubbers which are not recyclable owing to their thermosetting characteristics. TPE also require little or no compounding, with no need to add reinforcing agents, stabilizers or cure systems. Hence, batch-to-batch variations in weighting and metering components are absent, leading to improved consistency in both raw materials and fabricated articles. Depending on the environment, TPEs have outstanding thermal properties and material stability when exposed to a broad range of temperatures and non-polar materials.[1] TPEs consume less energy to produce, can be colored easily by most dyes, and allow economical quality control.
Processing
The two most important manufacturing methods with TPEs are extrusion and injection molding. Compression molding is seldom, if ever, used. Fabrication via injection molding is extremely rapid and highly economical. Both the equipment and methods normally used for the extrusion or injection molding of a conventional thermoplastic are generally suitable for TPEs. TPEs can also be processed by blow molding, melt calendaring,[3] thermoforming, and heat welding.
Applications
TPEs are used where conventional elastomers cannot provide the range of physical properties needed in the product. These materials find large application in the automotive sector and in household appliances sector. In 2014 the world market for TPEs reached a volume of ca. 16.7 billion US dollars. About 40% of all TPE products are used in the manufacturing of vehicles.[2] For instance copolyester TPEs are used in snowmobile tracks where stiffness and abrasion resistance are at a premium. They are also widely used for catheters where nylon block copolymers offer a range of softness ideal for patients. Thermoplastic silicon and olefin blends are used for extrusion of glass run and dynamic weatherstripping car profiles. Styrene block copolymers are used in shoe soles for their ease of processing, and widely as adhesives. TPE is commonly used to make suspension bushings for automotive performance applications because of its greater resistance to deformation when compared to regular rubber bushings. Thermoplastics have experienced growth in the heating, ventilation, and air conditioning (HVAC) industry due to the function, cost effectiveness and adaptability to modify plastic resins into a variety of covers, fans and housings. TPE may also be used in medical devices and is also finding more and more uses as an electrical cable jacket and inner insulation. You'll also be able to find TPE used in some headphone cables.
Footnotes
- 1 2 Levensalor, Alex. "The Benefits of Hytrel in Modern Belting". Retrieved 2016-10-27.
- 1 2 Market Study on Thermoplastic Elastomers, January 2015), by Ceresana
- ↑ "Processing methods for thermoplastic elastomers-TPE - Introduction". www.tut.fi. Retrieved 2016-10-27.
References
- PR Lewis and C Price, Polymer, 13, 20 (1972)
- Modern Plastic Mid-October Encyclopedia Issue, Introduction to TPEs, page:109-110