Polyethylene terephthalate
![]() | |
![]() | |
![]() | |
Names | |
---|---|
IUPAC name
Poly(ethyl benzene-1,4-dicarboxylate) | |
Identifiers | |
25038-59-9 ![]() | |
Abbreviations | PET, PETE |
ECHA InfoCard | 100.121.858 |
Properties | |
(C10H8O4)n[1] | |
Molar mass | variable |
Density | 1.38 g/cm3 (20 °C),[2] amorphous: 1.370 g/cm3,[1] single crystal: 1.455 g/cm3[1] |
Melting point | > 250 °C,[2] 260 °C[1] |
Boiling point | > 350 °C (decomposes) |
practically insoluble[2] | |
Thermal conductivity | 0.15[3] to 0.24 W m−1 K−1[1] |
Refractive index (nD) |
1.57–1.58,[3] 1.5750[1] |
Thermochemistry | |
1.0 kJ/(kg·K)[1] | |
Related compounds | |
Related Monomers |
Terephthalic acid Ethylene glycol |
Except where otherwise noted, data are given for materials in their standard state (at 25 °C [77 °F], 100 kPa). | |
![]() ![]() ![]() | |
Infobox references | |
Polyethylene terephthalate (sometimes written poly(ethylene terephthalate)), commonly abbreviated PET, PETE, or the obsolete PETP or PET-P, is the most common thermoplastic polymer resin of the polyester family and is used in fibers for clothing, containers for liquids and foods, thermoforming for manufacturing, and in combination with glass fiber for engineering resins.
It may also be referred to by the brand name Dacron; in Britain, Terylene;[4] or, in Russia and the former Soviet Union, Lavsan.
The majority of the world's PET production is for synthetic fibers (in excess of 60%), with bottle production accounting for about 30% of global demand.[5] In the context of textile applications, PET is referred to by its common name, polyester, whereas the acronym PET is generally used in relation to packaging. Polyester makes up about 18% of world polymer production and is the fourth-most-produced polymer; polyethylene (PE), polypropylene (PP) and polyvinyl chloride (PVC) are first, second and third, respectively.
PET consists of polymerized units of the monomer ethylene terephthalate, with repeating (C10H8O4) units. PET is commonly recycled, and has the number "1" as its recycling symbol.
Depending on its processing and thermal history, polyethylene terephthalate may exist both as an amorphous (transparent) and as a semi-crystalline polymer. The semicrystalline material might appear transparent (particle size < 500 nm) or opaque and white (particle size up to a few micrometers) depending on its crystal structure and particle size.
The monomer bis(2-hydroxyethyl) terephthalate can be synthesized by the esterification reaction between terephthalic acid and ethylene glycol with water as a byproduct, or by transesterification reaction between ethylene glycol and dimethyl terephthalate with methanol as a byproduct. Polymerization is through a polycondensation reaction of the monomers (done immediately after esterification/transesterification) with water as the byproduct.
Young's modulus (E) | 2800–3100 MPa |
Tensile strength(σt) | 55–75 MPa |
Elastic limit | 50–150% |
notch test | 3.6 kJ/m2 |
Glass transition temperature (Tg) | 67 to 81 °C |
Vicat B | 82 °C |
linear expansion coefficient (α) | 7×10−5/K |
Water absorption (ASTM) | 0.16 |
Source[1] |
Uses
Because PET is an excellent water and moisture barrier material, plastic bottles made from PET are widely used for soft drinks (see carbonation). For certain specialty bottles, such as those designated for beer containment, PET sandwiches an additional polyvinyl alcohol (PVOH) layer to further reduce its oxygen permeability.
Biaxially oriented PET film (often known by one of its trade names, "Mylar") can be aluminized by evaporating a thin film of metal onto it to reduce its permeability, and to make it reflective and opaque (MPET). These properties are useful in many applications, including flexible food packaging and thermal insulation. See: "space blankets". Because of its high mechanical strength, PET film is often used in tape applications, such as the carrier for magnetic tape or backing for pressure-sensitive adhesive tapes.
Non-oriented PET sheet can be thermoformed to make packaging trays and blister packs.[6] If crystallizable PET is used, the trays can be used for frozen dinners, since they withstand both freezing and oven baking temperatures. As opposed to amorphous PET, which is transparent, crystallizable PET or CPET tends to be black in colour.
When filled with glass particles or fibres, it becomes significantly stiffer and more durable.
PET is also used as a substrate in thin film solar cells.
Terylene (a trademark formed by inversion of (polyeth)ylene ter(ephthalate)) is also spliced into bell rope tops to help prevent wear on the ropes as they pass through the ceiling.
History
PET was patented in 1941 by John Rex Whinfield, James Tennant Dickson and their employer the Calico Printers' Association of Manchester, England. E. I. DuPont de Nemours in Delaware, USA, first used the trademark Mylar in June 1951 and received registration of it in 1952.[7] It is still the best-known name used for polyester film. The current owner of the trademark is DuPont Teijin Films US, a partnership with a Japanese company.[8]
In the Soviet Union, PET was first manufactured in the laboratories of the Institute of High-Molecular Compounds of the USSR Academy of Sciences in 1949, and its name "Lavsan" is an acronym thereof (лаборатории Института высокомолекулярных соединений Академии наук СССР).[9]
The PET bottle was patented in 1973 by Nathaniel Wyeth.[10]
Physical properties

PET in its natural state is a colorless, semi-crystalline resin. Based on how it is processed, PET can be semi-rigid to rigid, and it is very lightweight. It makes a good gas and fair moisture barrier, as well as a good barrier to alcohol (requires additional "barrier" treatment) and solvents. It is strong and impact-resistant. PET becomes white when exposed to chloroform and also certain other chemicals such as toluene.
About 60% crystallization is the upper limit for commercial products, with the exception of polyester fibers. Clear products can be produced by rapidly cooling molten polymer below Tg glass transition temperature to form an amorphous solid. Like glass, amorphous PET forms when its molecules are not given enough time to arrange themselves in an orderly, crystalline fashion as the melt is cooled. At room temperature the molecules are frozen in place, but, if enough heat energy is put back into them by heating above Tg, they begin to move again, allowing crystals to nucleate and grow. This procedure is known as solid-state crystallization.
When allowed to cool slowly, the molten polymer forms a more crystalline material. This material has spherulites containing many small crystallites when crystallized from an amorphous solid, rather than forming one large single crystal. Light tends to scatter as it crosses the boundaries between crystallites and the amorphous regions between them. This scattering means that crystalline PET is opaque and white in most cases. Fiber drawing is among the few industrial processes that produce a nearly single-crystal product.
Intrinsic viscosity
One of the most important characteristics of PET is referred to as intrinsic viscosity (IV).[11]
The intrinsic viscosity of the material, found by extrapolating to zero concentration of relative viscosity to concentration which is measured in deciliters per gram (dℓ/g). Intrinsic viscosity is dependent upon the length of its polymer chains but has no units due to being extrapolated to zero concentration. The longer the polymer chains the more entanglements between chains and therefore the higher the viscosity. The average chain length of a particular batch of resin can be controlled during polycondensation.
The intrinsic viscosity range of PET:[12]
Fiber grade
- 0.40–0.70 Textile
- 0.72–0.98 Technical, tire cord
Film grade
- 0.60–0.70 BoPET (biaxially oriented PET film)
- 0.70–1.00 Sheet grade for thermoforming
Bottle grade
- 0.70–0.78 Water bottles (flat)
- 0.78–0.85 Carbonated soft drink grade
Monofilament, engineering plastic
- 1.00–2.00
Drying
PET is hygroscopic, meaning that it absorbs water from its surroundings. However, when this "damp" PET is then heated, the water hydrolyzes the PET, decreasing its resilience. Thus, before the resin can be processed in a molding machine, it must be dried. Drying is achieved through the use of a desiccant or dryers before the PET is fed into the processing equipment.
Inside the dryer, hot dry air is pumped into the bottom of the hopper containing the resin so that it flows up through the pellets, removing moisture on its way. The hot wet air leaves the top of the hopper and is first run through an after-cooler, because it is easier to remove moisture from cold air than hot air. The resulting cool wet air is then passed through a desiccant bed. Finally, the cool dry air leaving the desiccant bed is re-heated in a process heater and sent back through the same processes in a closed loop. Typically, residual moisture levels in the resin must be less than 50 parts per million (parts of water per million parts of resin, by weight) before processing. Dryer residence time should not be shorter than about four hours. This is because drying the material in less than 4 hours would require a temperature above 160 °C, at which level hydrolysis would begin inside the pellets before they could be dried out.
PET can also be dried in compressed air resin dryers. Compressed air dryers do not reuse drying air. Dry, heated compressed air is circulated through the PET pellets as in the desiccant dryer, then released to the atmosphere.
Copolymers
In addition to pure (homopolymer) PET, PET modified by copolymerization is also available.
In some cases, the modified properties of copolymer are more desirable for a particular application. For example, cyclohexane dimethanol (CHDM) can be added to the polymer backbone in place of ethylene glycol. Since this building block is much larger (6 additional carbon atoms) than the ethylene glycol unit it replaces, it does not fit in with the neighboring chains the way an ethylene glycol unit would. This interferes with crystallization and lowers the polymer's melting temperature. In general, such PET is known as PETG or PET-G (Polyethylene terephthalate glycol-modified; Eastman Chemical, SK Chemicals, and Artenius Italia are some PETG manufacturers). PETG is a clear amorphous thermoplastic that can be injection molded or sheet extruded. It can be colored during processing.
Another common modifier is isophthalic acid, replacing some of the 1,4-(para-) linked terephthalate units. The 1,2-(ortho-) or 1,3-(meta-) linkage produces an angle in the chain, which also disturbs crystallinity.
Such copolymers are advantageous for certain molding applications, such as thermoforming, which is used for example to make tray or blister packaging from co-PET film, or amorphous PET sheet (A-PET) or PETG sheet. On the other hand, crystallization is important in other applications where mechanical and dimensional stability are important, such as seat belts. For PET bottles, the use of small amounts of isophthalic acid, CHDM, diethylene glycol (DEG) or other comonomers can be useful: if only small amounts of comonomers are used, crystallization is slowed but not prevented entirely. As a result, bottles are obtainable via stretch blow molding ("SBM"), which are both clear and crystalline enough to be an adequate barrier to aromas and even gases, such as carbon dioxide in carbonated beverages.
Production
Polyethylene terephthalate is produced from ethylene glycol and dimethyl terephthalate (C6H4(CO2CH3)2) or terephthalic acid.[13]
The former is a transesterification reaction, whereas the latter is an esterification reaction.
Dimethyl terephthalate process
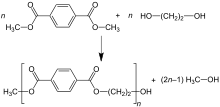
In dimethyl terephthalate process, this compound and excess ethylene glycol are reacted in the melt at 150–200 °C with a basic catalyst. Methanol (CH3OH) is removed by distillation to drive the reaction forward. Excess ethylene glycol is distilled off at higher temperature with the aid of vacuum. The second transesterification step proceeds at 270–280 °C, with continuous distillation of ethylene glycol as well.[13]
The reactions are idealized as follows:
- First step
- C6H4(CO2CH3)2 + 2 HOCH2CH2OH → C6H4(CO2CH2CH2OH)2 + 2 CH3OH
- Second step
- n C6H4(CO2CH2CH2OH)2 → [(CO)C6H4(CO2CH2CH2O)]n + n HOCH2CH2OH
Terephthalic acid process

In the terephthalic acid process, esterification of ethylene glycol and terephthalic acid is conducted directly at moderate pressure (2.7–5.5 bar) and high temperature (220–260 °C). Water is eliminated in the reaction, and it is also continuously removed by distillation:[13]
- n C6H4(CO2H)2 + n HOCH2CH2OH → [(CO)C6H4(CO2CH2CH2O)]n + 2n H2O
Degradation
PET is subjected to various types of degradations during processing. The main degradations that can occur are hydrolytic, and probably most important, thermal oxidation. When PET degrades, several things happen: discoloration, chain scissions resulting in reduced molecular weight, formation of acetaldehyde, and cross-links ("gel" or "fish-eye" formation). Discoloration is due to the formation of various chromophoric systems following prolonged thermal treatment at elevated temperatures. This becomes a problem when the optical requirements of the polymer are very high, such as in packaging applications. The thermal and thermooxidative degradation results in poor processibility characteristics and performance of the material.
One way to alleviate this is to use a copolymer. Comonomers such as CHDM or isophthalic acid lower the melting temperature and reduce the degree of crystallinity of PET (especially important when the material is used for bottle manufacturing). Thus, the resin can be plastically formed at lower temperatures and/or with lower force. This helps to prevent degradation, reducing the acetaldehyde content of the finished product to an acceptable (that is, unnoticeable) level. See copolymers, above. Another way to improve the stability of the polymer is to use stabilizers, mainly antioxidants such as phosphites. Recently, molecular level stabilization of the material using nanostructured chemicals has also been considered.
Acetaldehyde
Acetaldehyde is a colorless, volatile substance with a fruity smell. Although it forms naturally in some fruit, it can cause an off-taste in bottled water. Acetaldehyde forms by degradation of PET through the mishandling of the material. High temperatures (PET decomposes above 300 °C or 570 °F), high pressures, extruder speeds (excessive shear flow raises temperature), and long barrel residence times all contribute to the production of acetaldehyde. When acetaldehyde is produced, some of it remains dissolved in the walls of a container and then diffuses into the product stored inside, altering the taste and aroma. This is not such a problem for non-consumables (such as shampoo), for fruit juices (which already contain acetaldehyde), or for strong-tasting drinks like soft drinks. For bottled water, however, low acetaldehyde content is quite important, because, if nothing masks the aroma, even extremely low concentrations (10–20 parts per billion in the water) of acetaldehyde can produce an off-taste.
Antimony
Antimony (Sb) is a metalloid element that is used as a catalyst in the form of compounds such as antimony trioxide (Sb2O3) or antimony triacetate in the production of PET. After manufacturing, a detectable amount of antimony can be found on the surface of the product. This residue can be removed with washing. Antimony also remains in the material itself and can, thus, migrate out into food and drinks. Exposing PET to boiling or microwaving can increase the levels of antimony significantly, possibly above USEPA maximum contamination levels.[14] The drinking water limit assessed by WHO is 20 parts per billion (WHO, 2003), and the drinking water limit in the USA is 6 parts per billion.[15] Although antimony trioxide is of low toxicity when taken orally,[16] its presence is still of concern. The Swiss Federal Office of Public Health investigated the amount of antimony migration, comparing waters bottled in PET and glass: The antimony concentrations of the water in PET bottles were higher, but still well below the allowed maximum concentration. The Swiss Federal Office of Public Health concluded that small amounts of antimony migrate from the PET into bottled water, but that the health risk of the resulting low concentrations is negligible (1% of the "tolerable daily intake" determined by the WHO). A later (2006) but more widely publicized study found similar amounts of antimony in water in PET bottles.[17] The WHO has published a risk assessment for antimony in drinking water.[16]
Fruit juice concentrates (for which no guidelines are established), however, that were produced and bottled in PET in the UK were found to contain up to 44.7 µg/L of antimony, well above the EU limits for tap water of 5 µg/L.[18][19]
Biodegradation
At least one species of bacterium in the genus Nocardia can degrade PET with an esterase enzyme.[20]
Japanese scientists have isolated a bacterium Ideonella sakaiensis that possesses two enzymes which can break down the PET into smaller pieces that the bacterium can digest. A colony of I. sakaiensis can disintegrate a plastic film in about six weeks.[21][22]
Safety
Commentary published in Environmental Health Perspectives in April 2010 suggested that PET might yield endocrine disruptors under conditions of common use and recommended research on this topic.[23] Proposed mechanisms include leaching of phthalates as well as leaching of antimony. Article published in Journal of Environmental Monitoring in April 2012 concludes that antimony concentration in deionized water stored in PET bottles stays within EU's acceptable limit even if stored briefly at temperatures up to 60 °C (140 °F), while bottled contents (water or soft drinks) may occasionally exceed the EU limit after less than a year of storage at room temperature.[24]
Bottle processing equipment

There are two basic molding methods for PET bottles, one-step and two-step. In two-step molding, two separate machines are used. The first machine injection molds the preform, which resembles a test tube, with the bottle-cap threads already molded into place. The body of the tube is significantly thicker, as it will be inflated into its final shape in the second step using stretch blow molding.
In the second step, the preforms are heated rapidly and then inflated against a two-part mold to form them into the final shape of the bottle. Preforms (uninflated bottles) are now also used as robust and unique containers themselves; besides novelty candy, some Red Cross chapters distribute them as part of the Vial of Life program to homeowners to store medical history for emergency responders. Another increasingly common use for the preforms are containers in the outdoor activity geocaching.
In one-step machines, the entire process from raw material to finished container is conducted within one machine, making it especially suitable for molding non-standard shapes (custom molding), including jars, flat oval, flask shapes, etc. Its greatest merit is the reduction in space, product handling and energy, and far higher visual quality than can be achieved by the two-step system.
Polyester recycling industry
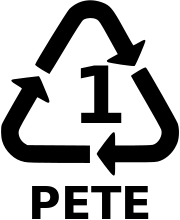
In year 2016, it was estimated that 56 million tons of PET are produced each year.[25]]]
While most thermoplastics can, in principle, be recycled, PET bottle recycling is more practical than many other plastic applications because of the high value of the resin and the almost exclusive use of PET for widely used water and carbonated soft drink bottling. PET has a resin identification code of 1.[26] The prime uses for recycled PET are polyester fiber, strapping, and non-food containers.[26]
Because of the recyclability of PET and the relative abundance of post-consumer waste in the form of bottles, PET is rapidly gaining market share as a carpet fiber. Mohawk Industries released everSTRAND in 1999, a 100% post-consumer recycled content PET fiber. Since that time, more than 17 billion bottles have been recycled into carpet fiber.[27] Pharr Yarns, a supplier to numerous carpet manufacturers including Looptex, Dobbs Mills, and Berkshire Flooring,[28] produces a BCF (bulk continuous filament) PET carpet fiber containing a minimum of 25% post-consumer recycled content.
PET, as with many plastics, is also an excellent candidate for thermal disposal (incineration), as it is composed of carbon, hydrogen, and oxygen, with only trace amounts of catalyst elements (but no sulfur). PET has the energy content of soft coal.
When recycling polyethylene terephthalate or PET or polyester, in general two ways have to be differentiated:
- The chemical recycling back to the initial raw materials purified terephthalic acid (PTA) or dimethyl terephthalate (DMT) and ethylene glycol (EG) where the polymer structure is destroyed completely, or in process intermediates like bis(2-hydroxyethyl) terephthalate
- The mechanical recycling where the original polymer properties are being maintained or reconstituted.
Chemical recycling of PET will become cost-efficient only applying high capacity recycling lines of more than 50,000 tons/year. Such lines could only be seen, if at all, within the production sites of very large polyester producers. Several attempts of industrial magnitude to establish such chemical recycling plants have been made in the past but without resounding success. Even the promising chemical recycling in Japan has not become an industrial breakthrough so far. The two reasons for this are: at first, the difficulty of consistent and continuous waste bottles sourcing in such a huge amount at one single site, and, at second, the steadily increased prices and price volatility of collected bottles. The prices of baled bottles increased for instance between the years 2000 and 2008 from about 50 Euro/ton to over 500 Euro/ton in 2008.
Mechanical recycling or direct circulation of PET in the polymeric state is operated in most diverse variants today. These kinds of processes are typical of small and medium-size industry. Cost-efficiency can already be achieved with plant capacities within a range of 5000–20,000 tons/year. In this case, nearly all kinds of recycled-material feedback into the material circulation are possible today. These diverse recycling processes are being discussed hereafter in detail.
Besides chemical contaminants and degradation products generated during first processing and usage, mechanical impurities are representing the main part of quality depreciating impurities in the recycling stream. Recycled materials are increasingly introduced into manufacturing processes, which were originally designed for new materials only. Therefore, efficient sorting, separation and cleaning processes become most important for high quality recycled polyester.
When talking about polyester recycling industry, we are concentrating mainly on recycling of PET bottles, which are meanwhile used for all kinds of liquid packaging like water, carbonated soft drinks, juices, beer, sauces, detergents, household chemicals and so on. Bottles are easy to distinguish because of shape and consistency and separate from waste plastic streams either by automatic or by hand-sorting processes. The established polyester recycling industry consists of three major sections:
- PET bottle collection and waste separation: waste logistics
- Production of clean bottle flakes: flake production
- Conversion of PET flakes to final products: flake processing
Intermediate product from the first section is baled bottle waste with a PET content greater than 90%. Most common trading form is the bale but also bricked or even loose, pre-cut bottles are common in the market. In the second section, the collected bottles are converted to clean PET bottle flakes. This step can be more or less complex and complicated depending on required final flake quality. During the third step, PET bottle flakes are processed to any kind of products like film, bottles, fiber, filament, strapping or intermediates like pellets for further processing and engineering plastics.
Besides this external (post-consumer) polyester bottle recycling, numbers of internal (pre-consumer) recycling processes exist, where the wasted polymer material does not exit the production site to the free market, and instead is reused in the same production circuit. In this way, fiber waste is directly reused to produce fiber, preform waste is directly reused to produce preforms, and film waste is directly reused to produce film.
PET bottle recycling
Purification and decontamination
The success of any recycling concept is hidden in the efficiency of purification and decontamination at the right place during processing and to the necessary or desired extent.
In general, the following applies: The earlier in the process foreign substances are removed, and the more thoroughly this is done, the more efficient the process is.
The high plasticization temperature of PET in the range of 280 °C (536 °F) is the reason why almost all common organic impurities such as PVC, PLA, polyolefin, chemical wood-pulp and paper fibers, polyvinyl acetate, melt adhesive, coloring agents, sugar, and protein residues are transformed into colored degradation products that, in their turn, might release in addition reactive degradation products. Then, the number of defects in the polymer chain increases considerably. The particle size distribution of impurities is very wide, the big particles of 60–1000 µm—which are visible by naked eye and easy to filter—representing the lesser evil, since their total surface is relatively small and the degradation speed is therefore lower. The influence of the microscopic particles, which —because they are many— increase the frequency of defects in the polymer, is relatively greater.
The motto "What the eye does not see the heart cannot grieve over" is considered to be very important in many recycling processes. Therefore, besides efficient sorting, the removal of visible impurity particles by melt filtration processes plays a particular part in this case.



In general, one can say that the processes to make PET bottle flakes from collected bottles are as versatile as the different waste streams are different in their composition and quality. In view of technology there isn't just one way to do it. Meanwhile, there are many engineering companies that are offering flake production plants and components, and it is difficult to decide for one or other plant design. Nevertheless, there are processes that are sharing most of these principles. Depending on composition and impurity level of input material, the general following process steps are applied.[29]
- Bale opening, briquette opening
- Sorting and selection for different colors, foreign polymers especially PVC, foreign matter, removal of film, paper, glass, sand, soil, stones, and metals
- Pre-washing without cutting
- Coarse cutting dry or combined to pre-washing
- Removal of stones, glass, and metal
- Air sifting to remove film, paper, and labels
- Grinding, dry and / or wet
- Removal of low-density polymers (cups) by density differences
- Hot-wash
- Caustic wash, and surface etching, maintaining intrinsic viscosity and decontamination
- Rinsing
- Clean water rinsing
- Drying
- Air-sifting of flakes
- Automatic flake sorting
- Water circuit and water treatment technology
- Flake quality control
Impurities and material defects
The number of possible impurities and material defects that accumulate in the polymeric material is increasing permanently—when processing as well as when using polymers—taking into account a growing service lifetime, growing final applications and repeated recycling. As far as recycled PET bottles are concerned, the defects mentioned can be sorted in the following groups:
- Reactive polyester OH- or COOH- end groups are transformed into dead or non-reactive end groups, e.g. formation of vinyl ester end groups through dehydration or decarboxylation of terephthalate acid, reaction of the OH- or COOH- end groups with mono-functional degradation products like mono-carbonic acids or alcohols. Results are decreased reactivity during re-polycondensation or re-SSP and broadening the molecular weight distribution.
- The end group proportion shifts toward the direction of the COOH end groups built up through a thermal and oxidative degradation. The results are decrease in reactivity, and increase in the acid autocatalytic decomposition during thermal treatment in presence of humidity.
- Number of polyfunctional macromolecules increases. Accumulation of gels and long-chain branching defects.
- Number, concentration, and variety of nonpolymer-identical organic and inorganic foreign substances are increasing. With every new thermal stress, the organic foreign substances will react by decomposition. This is causing the liberation of further degradation-supporting substances and coloring substances.
- Hydroxide and peroxide groups build up at the surface of the products made of polyester in presence of air (oxygen) and humidity. This process is accelerated by ultraviolet light. During an ulterior treatment process, hydro peroxides are a source of oxygen radicals, which are source of oxidative degradation. Destruction of hydro peroxides is to happen before the first thermal treatment or during plasticization and can be supported by suitable additives like antioxidants.
Taking into consideration the above-mentioned chemical defects and impurities, there is an ongoing modification of the following polymer characteristics during each recycling cycle, which are detectable by chemical and physical laboratory analysis.
In particular:
- Increase of COOH end-groups
- Increase of color number b
- Increase of haze (transparent products)
- Increase of oligomer content
- Reduction in filterability
- Increase of by-products content such as acetaldehyde, formaldehyde
- Increase of extractable foreign contaminants
- Decrease in color L
- Decrease of intrinsic viscosity or dynamic viscosity
- Decrease of crystallization temperature and increase of crystallization speed
- Decrease of the mechanical properties like tensile strength, elongation at break or elastic modulus
- Broadening of molecular weight distribution
The recycling of PET-bottles is meanwhile an industrial standard process that is offered by a wide variety of engineering companies.[30]
Processing examples for recycled polyester
Recycling processes with polyester are almost as varied as the manufacturing processes based on primary pellets or melt. Depending on purity of the recycled materials, polyester can be used today in most of the polyester manufacturing processes as blend with virgin polymer or increasingly as 100% recycled polymer. Some exceptions like BOPET-film of low thickness, special applications like optical film or yarns through FDY-spinning at > 6000 m/min, microfilaments, and micro-fibers are produced from virgin polyester only.
Simple re-pelletizing of bottle flakes
This process consists of transforming bottle waste into flakes, by drying and crystallizing the flakes, by plasticizing and filtering, as well as by pelletizing. Product is an amorphous re-granulate of an intrinsic viscosity in the range of 0.55–0.7 dℓ/g, depending on how complete pre-drying of PET flakes has been done.
Special feature are: Acetaldehyde and oligomers are contained in the pellets at lower level; the viscosity is reduced somehow, the pellets are amorphous and have to be crystallized and dried before further processing.
Processing to:
- A-PET film for thermoforming
- Addition to PET virgin production
- BoPET packaging film
- PET Bottle resin by SSP
- Carpet yarn
- Engineering plastic
- Filaments
- Non-woven
- Packaging stripes
- Staple fibre.
Choosing the re-pelletizing way means having an additional conversion process that is, at the one side, energy-intensive and cost-consuming, and causes thermal destruction. At the other side, the pelletizing step is providing the following advantages:
- Intensive melt filtration
- Intermediate quality control
- Modification by additives
- Product selection and separation by quality
- Processing flexibility increased
- Quality uniformization.
Manufacture of PET-pellets or flakes for bottles (bottle to bottle) and A-PET
This process is, in principle, similar to the one described above; however, the pellets produced are directly (continuously or discontinuously) crystallized and then subjected to a solid-state polycondensation (SSP) in a tumbling drier or a vertical tube reactor. During this processing step, the corresponding intrinsic viscosity of 0.80–0.085 dℓ/g is rebuild again and, at the same time, the acetaldehyde content is reduced to < 1 ppm.
The fact that some machine manufacturers and line builders in Europe and USA make efforts to offer independent recycling processes, e.g. the so-called bottle-to-bottle (B-2-B) process, such as BePET, Starlinger, URRC or BÜHLER, aims at generally furnishing proof of the "existence" of the required extraction residues and of the removal of model contaminants according to FDA applying the so-called challenge test, which is necessary for the application of the treated polyester in the food sector. Besides this process approval it is nevertheless necessary that any user of such processes has to constantly check the FDA-limits for the raw materials manufactured by himself for his process.
Direct conversion of bottle flakes
In order to save costs, an increasing number of polyester intermediate producers like spinning mills, strapping mills, or cast film mills are working on the direct use of the PET-flakes, from the treatment of used bottles, with a view to manufacturing an increasing number of polyester intermediates. For the adjustment of the necessary viscosity, besides an efficient drying of the flakes, it is possibly necessary to also reconstitute the viscosity through polycondensation in the melt phase or solid-state polycondensation of the flakes. The latest PET flake conversion processes are applying twin screw extruders, multi-screw extruders or multi-rotation systems and coincidental vacuum degassing to remove moisture and avoid flake pre-drying. These processes allow the conversion of undried PET flakes without substantial viscosity decrease caused by hydrolysis.
With regard to the consumption of PET bottle flakes, the main portion of about 70% is converted to fibers and filaments. When using directly secondary materials such as bottle flakes in spinning processes, there are a few processing principles to obtain.
High-speed spinning processes for the manufacture of POY normally need a viscosity of 0.62–0.64 dℓ/g. Starting from bottle flakes, the viscosity can be set via the degree of drying. The additional use of TiO2 is necessary for full dull or semi dull yarn. In order to protect the spinnerets, an efficient filtration of the melt is, in any case is necessary. For the time-being, the amount of POY made of 100% recycling polyester is rather low because this process requires high purity of spinning melt. Most of the time, a blend of virgin and recycled pellets is used.
Staple fibers are spun in an intrinsic viscosity range that lies rather somewhat lower and that should be between 0.58 and 0.62 dℓ/g. In this case, too, the required viscosity can be adjusted via drying or vacuum adjustment in case of vacuum extrusion. For adjusting the viscosity, however, an addition of chain length modifier like ethylene glycol or diethylene glycol can also be used.
Spinning non-woven—in the fine titer field for textile applications as well as heavy spinning non-woven as basic materials, e.g. for roof covers or in road building—can be manufactured by spinning bottle flakes. The spinning viscosity is again within a range of 0.58–0.65 dℓ/g.
One field of increasing interest where recycled materials are used is the manufacture of high-tenacity packaging stripes, and monofilaments. In both cases, the initial raw material is a mainly recycled material of higher intrinsic viscosity. High-tenacity packaging stripes as well as monofilament are then manufactured in the melt spinning process.
Recycling to the monomers
Polyethylene terephthalate can be depolymerized to yield the constituent monomers. After purification, the monomers can be used to prepare new polyethylene terephthalate. The ester bonds in polyethylene terephthalate may be cleaved by hydrolysis, or by transesterification. The reactions are simply the reverse of those used in production.
Partial glycolysis
Partial glycolysis (transesterification with ethylene glycol) converts the rigid polymer into short-chained oligomers that can be melt-filtered at low temperature. Once freed of the impurities, the oligomers can be fed back into the production process for polymerization.
The task consists in feeding 10–25% bottle flakes while maintaining the quality of the bottle pellets that are manufactured on the line. This aim is solved by degrading the PET bottle flakes—already during their first plasticization, which can be carried out in a single- or multi-screw extruder—to an intrinsic viscosity of about 0.30 dℓ/g by adding small quantities of ethylene glycol and by subjecting the low-viscosity melt stream to an efficient filtration directly after plasticization. Furthermore, temperature is brought to the lowest possible limit. In addition, with this way of processing, the possibility of a chemical decomposition of the hydro peroxides is possible by adding a corresponding P-stabilizer directly when plasticizing. The destruction of the hydro peroxide groups is, with other processes, already carried out during the last step of flake treatment for instance by adding H3PO3.[31] The partially glycolyzed and finely filtered recycled material is continuously fed to the esterification or prepolycondensation reactor, the dosing quantities of the raw materials are being adjusted accordingly.
Total glycolysis, methanolysis, and hydrolysis
The treatment of polyester waste through total glycolysis to fully convert the polyester to bis(2-hydroxyethyl) terephthalate (C6H4(CO2CH2CH2OH)2). This compound is purified by vacuum distillation, and is one of the intermediates used in polyester manufacture (see production). The reaction involved is as follows:
- [(CO)C6H4(CO2CH2CH2O)]n + n HOCH2CH2OH → n C6H4(CO2CH2CH2OH)2
This recycling route has been executed on an industrial scale in Japan as experimental production.
Similar to total glycolysis, methanolysis converts the polyester to dimethyl terephthalate, which can be filtered and vacuum distilled:
- [(CO)C6H4(CO2CH2CH2O)]n + 2n CH3OH → n C6H4(CO2CH3)2
Methanolysis is only rarely carried out in industry today because polyester production based on dimethyl terephthalate has shrunk tremendously, and many dimethyl terephthalate producers have disappeared.[32]
Also as above, polyethylene terephthalate can be hydrolyzed to terephthalic acid and ethylene glycol under high temperature and pressure. The resultant crude terephthalic acid can be purified by recrystallization to yield material suitable for re-polymerization:
- [(CO)C6H4(CO2CH2CH2O)]n + 2n H2O → n C6H4(CO2H)2 + n HOCH2CH2OH
This method does not appear to have been commercialized yet.
See also
- BoPET (biaxially oriented PET)
- Bioplastic
- Plastic recycling
- Polyester
- PET bottle recycling
- Solar water disinfection—a method of disinfecting water using only sunlight and plastic PET bottles
- Polycyclohexylenedimethylene terephthalate—a polyester with a similar structure as PET
References
- 1 2 3 4 5 6 7 8 A.K. van der Vegt & L.E. Govaert, Polymeren, van keten tot kunstof, ISBN 90-407-2388-5
- 1 2 3 Record of Polyethylenterephthalat in the GESTIS Substance Database of the IFA, accessed on 7 November 2007
- 1 2 Speight, J. G. and Lange, Norbert Adolph (2005). McGraw-Hill, ed. Lange's handbook of chemistry (16 ed.). pp. 2.807–2.758. ISBN 0-07-143220-5.
- ↑ The name Terylene was formed by inversion of (polyeth)ylene ter(ephthalate) and dates to the 1940s. Oxford Dictionary. Terylene was first registered as a UK trademark in April 1946. UK Intellectual Property Office UK00000646992
- ↑ Ji, Li Na (June 2013). "Study on Preparation Process and Properties of Polyethylene Terephthalate (PET)". Applied Mechanics and Materials. 312: 406–410.
- ↑ Pasbrig, Erwin (Mar 29, 2007), Cover film for blister packs, retrieved 2016-11-20
- ↑ John Rex Whinfield and James Tennant Dickson (1941) "Improvements Relating to the Manufacture of Highly Polymeric Substances", UK Patent 578,079; "Polymeric Linear Terephthalic Esters", U.S. Patent 2,465,319 Publication date: 22 March 1949; Filing date: 24 September 1945; Priority date: 29 July 1941
- ↑ TEIJIN: Trademarks "Mylar and Melinex are the registered trademarks or trademarks of Dupont Teijin Films U.S. Limited Partnership and have been licensed to Teijin DuPont Films Japan Limited"
- ↑
- ↑ Nathaniel C. Wyeth "Biaxially Oriented Poly(ethylene terephthalate) Bottle" US patent 3733309, Issued May 1973
- ↑ Ulrich K. Thiele (2007) Polyester Bottle Resins, Production, Processing, Properties and Recycling, Heidelberg, Germany, pp. 85 ff, ISBN 978-3-9807497-4-9
- ↑ V.B. Gupta and Z. Bashir (2002) Chapter 7, p. 320 in Stoyko Fakirov (ed.) Handbook of Thermoplastic Polyesters, Wiley-VCH, Weinheim, ISBN 3-527-30113-5.
- 1 2 3 "Polyesters", Ullmann's Encyclopedia of Industrial Chemistry, A21, Weinheim: Wiley-VCH, 2005, pp. 233–238, doi:10.1002/14356007.a21_227
- ↑ Cheng, X.; et al. (2010). "Assessment of metal contaminations leaching out from recycling plastic bottles upon treatments". Environmental science and pollution research international. 17 (7): 1323–30. doi:10.1007/s11356-010-0312-4. PMID 20309737.
- ↑ Consumer Factsheet on: Antimony, EPA archive 2003-06-23
- 1 2 Guidelines for drinking – water quality. who.int
- ↑ Shotyk, William; et al. (2006). "Contamination of Canadian and European bottled waters with antimony from PET containers". Journal of Environmental Monitoring. 8 (2): 288–92. doi:10.1039/b517844b. PMID 16470261.
- ↑ Hansen, Claus; et al. (2010). "Elevated antimony concentrations in commercial juices". Journal of Environmental Monitoring. 12 (4): 822–4. doi:10.1039/b926551a. PMID 20383361.
- ↑ Borland, Sophie (1 March 2010). "Fruit juice cancer warning as scientists find harmful chemical in 16 drinks". Daily Mail.
- ↑ Sharon, Chetna; Sharon, Madhuri (2012). "Studies on Biodegradation of Polyethylene terephthalate: A synthetic polymer" (PDF). Journal of Microbiology and Biotechnology Research. pp. 248–257.
- ↑ "A bacterium that degrades and assimilates poly(ethylene terephthalate)". Science. 11 March 2016. Retrieved 11 March 2016.
- ↑ "Could a new plastic-eating bacteria help combat this pollution scourge?". The Guardian. 10 March 2016. Retrieved 11 March 2016.
- ↑ Sax, Leonard (2010). "Polyethylene Terephthalate May Yield Endocrine Disruptors". Environmental Health Perspectives. 118 (4): 445–8. doi:10.1289/ehp.0901253. PMC 2854718
. PMID 20368129.
- ↑ Tukur, Aminu (2012). "PET bottle use patterns and antimony migration into bottled water and soft drinks: the case of British and Nigerian bottles". Journal of Environmental Monitoring. 14 (4): 1236–1246. doi:10.1039/C2EM10917D.
- ↑ Saxena, Shalini (19 March 2016). "Newly identified bacteria cleans up common plastic". Ars Technica. Retrieved 21 March 2016.
- 1 2 "Plastic Packaging Resins" (PDF). American Chemistry Council.
- ↑ everSTRAND™ Carpet-inspectors-experts.com archive 2008-03-17
- ↑ Simply Green Carpet – A Berkshire Flooring Brand. simplygreencarpet.com
- ↑ PET-Recycling Forum; "Current Technological Trends in Polyester Recycling"; 9th International Polyester Recycling Forum Washington, 2006; São Paulo; ISBN 3-00-019765-6
- ↑ Ulrich K. Thiele (2007) Polyester Bottle Resins Production, Processing, Properties and Recycling, PETplanet Publisher GmbH, Heidelberg, Germany, pp. 259 ff, ISBN 978-3-9807497-4-9
- ↑ Frank Boos, Ulrich Dr Thiele, "Reprocessing pulverised polyester waste without yellowing", German Patent DE19503055, Publication date: 8 August 1996
- ↑ Stoyko Fakirov (ed.) (2002) Handbook of Thermoplastic Polyesters, Wiley-VCH, Weinheim, pp. 1223 ff, ISBN 3-527-30113-5
External links
![]() |
Wikimedia Commons has media related to Polyethylene terephthalate. |
- American Plastics Council: PlasticInfo.org
- KenPlas Industry Ltd.: "What is PET (Polyethylene Terephthalate)"
- "WAVE Polymer Technology: PET (Polyethylene Terephthalate) flakes processing"