Continuously variable transmission
Transmission types |
---|
Manual |
Automatic |
Bicycle gearing |
A continuously variable transmission (CVT) (also known as a single-speed transmission, stepless transmission, pulley transmission, or, in case of motorcycles, a twist-and-go) is an automatic transmission that can change seamlessly through a continuous range of effective gear ratios. This contrasts with other mechanical transmissions that offer a fixed number of gear ratios. The flexibility of a CVT allows the input shaft to maintain a constant angular velocity.
A belt-driven design offers approximately 88% efficiency,[1] which, while lower than that of a manual transmission, can be offset by lower production cost and by enabling the engine to run at its most efficient speed for a range of output speeds. When power is more important than economy, the ratio of the CVT can be changed to allow the engine to turn at the RPM at which it produces greatest power. This is typically higher than the RPM that achieves peak efficiency. In low-mass low-torque applications (such as motor scooters) a belt-driven CVT also offers ease of use and mechanical simplicity
A CVT does not strictly require the presence of a clutch. Nevertheless, in some vehicles (e.g. motorcycles), a centrifugal clutch is added[2] to facilitate a "neutral" stance, which is useful when idling or manually reversing into a parking space.
Uses
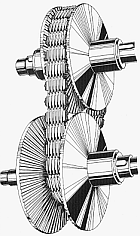
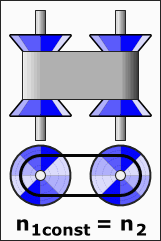
Simple rubber belt CVTs are commonly used in small motorized vehicles, where their mechanical simplicity and ease of use outweigh their comparative inefficiency. Nearly all snowmobiles, utility vehicles, golf carts and motor scooters use CVTs, typically the rubber belt or variable pulley variety. Many small tractors and self-propelled mowers for home and garden also use simple rubber belt CVT, though hydrostatic systems are more common.
Hydrostatic CVTs are common in small to medium-sized agricultural and earthmoving equipment. As the engines in these machines are typically run at constant power settings to provide hydraulic power or to power machinery, losses in mechanical efficiency are offset by enhanced operational efficiency, such as reduced forward-reverse shuttle times in earthmoving operations. Transmission output is varied to control both travel speed and direction. This is particularly beneficial in equipment designed to pivot or skid steer through differential power application as the required differential steering action can easily be supplied by independent CVTs, allowing steering to be accomplished without braking losses or loss of tractive effort and allowing the machine to pivot in place. In mowing or harvesting operations a CVT allows the forward speed of the tractor or combine harvester to be adjusted independently of the engine speed. This allows the operator to slow or accelerate as needed to accommodate variations in thickness of the crop.
CVTs have been used in aircraft electrical power generating systems since the 1950s and in Sports Car Club of America (SCCA) Formula 500 race cars since the early 1970s. CVTs were banned from Formula 1 in 1994 because of concerns that the best-funded teams would dominate if they managed to create a viable F1 CVT.[3] More recently, CVT systems have been developed for go-karts and have proven to increase performance and engine life expectancy. The Tomcar range of off-road vehicles also utilizes the CVT system.
Some drill presses and milling machines contain a pulley-based CVT where the output shaft has a pair of manually adjustable conical pulley halves through which a wide drive belt from the motor loops. The pulley on the motor, however, is usually fixed in diameter, or may have a series of given-diameter steps to allow a selection of speed ranges. A handwheel on the drill press, marked with a scale corresponding to the desired machine speed, is mounted to a reduction gearing system for the operator to precisely control the width of the gap between the pulley halves. This gap width thus adjusts the gearing ratio between the motor's fixed pulley and the output shaft's variable pulley, changing speed of the chuck. A tensioner pulley is implemented in the belt transmission to take up or release the slack in the belt as the speed is altered. In most cases, the speed must be changed with the motor running.
CVTs should be distinguished from power-sharing transmissions (PSTs), as used in newer hybrid cars, such as the Toyota Prius, Highlander and Camry, the Nissan Altima, and newer-model Ford Escape Hybrid SUVs. CVT technology uses only one input from a prime mover and delivers variable output speeds and torque, whereas PST technology uses two prime mover inputs and varies the ratio of their contributions to output speed and power. These transmissions are fundamentally different.
Some vehicles that offer CVT are the Ford C-MAX hybrid, the Mitsubishi Lancer, the Dodge Caliber, the Toyota Corolla, the Scion iQ, the Honda Insight, Fit, CR-Z hybrid, CR-V, Capa, Honda Civic, Honda Accord, the Nissan Tiida/Versa (SL, SV, and Note S Plus or higher models), Cube, Juke, Sentra, Altima, Maxima, 2013 1.2 Note, Rogue, X-Trail, Murano, Pathfinder, Sunny and the non-Mexican Micra, the Jeep Patriot and Compass, the Suzuki SX4 S-Cross, and the Subaru Forester, Impreza, Legacy, and Outback, toyota Allion 2009 onwards, Toyota Premio 2009 onwards, toyota avalon, toyota mark X etc.
Types
Variable-diameter pulley (VDP) or Reeves drive
In this most common CVT system,[4] there are two V-belt pulleys that are split perpendicular to their axes of rotation, with a V-belt running between them. The gear ratio is changed by moving the two sheaves of one pulley closer together and the two sheaves of the other pulley farther apart. The V-shaped cross section of the belt causes it to ride higher on one pulley and lower on the other. This changes the effective diameters of both pulleys, which changes the overall gear ratio. As the distance between the pulleys and the length of the belt does not change both pulleys must be adjusted (one bigger, the other smaller) simultaneously in order to maintain the proper amount of tension on the belt. Simple CVTs combining a centrifugal drive pulley with a spring loaded driven pulley often use belt tension to effect the conforming adjustments in the driven pulley. The V-belt needs to be very stiff in the pulley's axial direction in order to make only short radial movements while sliding in and out of the pulleys.
Steel reinforced v-belts are sufficient for low-mass low-torque applications like utility vehicles and snowmobiles but higher mass and torque applications such as automobiles require a chain. Each element of the chain must have conical sides that fit the pulley when the belt is running on the outermost radius. As the chain moves into the pulleys the contact area gets smaller. As the contact area is proportional to the number of elements, chain belts require lots of very small elements. The shape of the elements is governed by the static of a column. The pulley-radial thickness of the belt is a compromise between maximum gear ratio and torque. For the same reason the axis between the pulleys is as thin as possible. In a chain-based cvt a film of lubricant is applied to the pulleys. It needs to be thick enough so that the pulley and the chain never touch and it must be thin in order not to waste power when each element dives into the lubrication film. Additionally, the chain elements stabilize about 12 steel bands. Each band is thin enough so that it bends easily. If bending, it has a perfect conical surface on its side. In the stack of bands each band corresponds to a slightly different gear ratio, and thus they slide over each other and need oil between them. Also the outer bands slide through the stabilizing chain, while the center band can be used as the chain linkage.[note 1]

Toroidal or roller-based (Extroid)
Vigneshraj M Toroidal CVTs are made up of discs and rollers that transmit power between the discs. The discs can be pictured as two almost conical parts, point to point, with the sides dished such that the two parts could fill the central hole of a torus. One disc is the input, and the other is the output. Between the discs are rollers which vary the ratio and which transfer power from one side to the other. When the roller's axis is perpendicular to the axis of the near-conical parts, it contacts the near-conical parts at same-diameter locations and thus gives a 1:1 gear ratio. The roller can be moved along the axis of the near-conical parts, changing angle as needed to maintain contact. This will cause the roller to contact the near-conical parts at varying and distinct diameters, giving a gear ratio of something other than 1:1. Systems may be partial or full toroidal. Full toroidal systems are the most efficient design while partial toroidals may still require a torque converter, and hence lose efficiency.
Some toroidal systems are also infinitely variable, and the direction of thrust can be reversed within the CVT.[5]
Diagrams:
Examples:
- Nissan Extroid CVT (pdf on Nissan-Global site)
- Torotrak
Magnetic or m
Vigneshraj M -
A magnetic continuous variable transmission system was developed at the University of Sheffield in 2006 and later commercialized.[6] mCVT is a variable magnetic transmission which gives an electrically controllable gear ratio. It can act as a power split device and can match a fixed input speed from a prime-mover to a variable load by importing/exporting electrical power through a variator path. The mCVT is of particular interest as a highly efficient power-split device for blended parallel hybrid vehicles, but also has potential applications in renewable energy, marine propulsion and industrial drive sectors.
Infinitely variable transmission (IVT)
A subset of CVT designs are called infinitely variable transmissions (IVT or IVTs), in which the range of ratios of output shaft speed to input shaft speed includes a zero ratio that can be continuously approached from a defined "higher" ratio. A zero output speed (low gear) with a finite input speed implies an infinite input-to-output speed ratio, which can be continuously approached from a given finite input value with an IVT. Low gears are a reference to low ratios of output speed to input speed. This low ratio is taken to the extreme with IVTs, resulting in a "neutral", or non-driving "low" gear limit, in which the output speed is zero. Unlike neutral in a normal automotive transmission, IVT output rotation may be prevented because the backdriving (reverse IVT operation) ratio may be infinite, resulting in impossibly high backdriving torque; in a ratcheting IVT, however, the output may freely rotate in the forward direction.
In the early decades of the 20th century, several tractors and small locomotives were built with friction-disk transmissions with an output disk rolling on the face of the input disk. For disks of identical diameter, the effective gear ratio could be varied from 1:1 when the point of contact was at the perimeter of the input disk, to infinity when the point of contact was at the center, to -1:1 when the point of contact was at the opposite extreme. The transmission on early Plymouth locomotives worked this way, while on tractors using friction disks, the range of reverse speeds was typically limited.[7]
The ratcheting IVT dates back to before the 1930s; the original design converts rotary motion to oscillating motion and back to rotary motion using roller clutches.[8] The stroke of the intermediate oscillations is adjustable, varying the output speed of the shaft. This original design is still manufactured today, and an example and animation of this IVT can be found here.[9] Paul B. Pires created a more compact (radially symmetric) variation that employs a ratchet mechanism instead of roller clutches, so it doesn't have to rely on friction to drive the output. An article and sketch of this variation can be found here [10]
Many IVTs result from the combination of a CVT with a planetary gear system which enforces an IVT output shaft rotation speed which is equal to the difference between two other speeds within the IVT. This IVT configuration uses its CVT as a continuously variable regulator (CVR) of the rotation speed of any one of the three rotators of the planetary gear system (PGS). If two of the PGS rotator speeds are the input and output of the CVR, there is a setting of the CVR that results in the IVT output speed of zero. The maximum output/input ratio can be chosen from infinite practical possibilities through selection of additional input or output gear, pulley or sprocket sizes without affecting the zero output or the continuity of the whole system. The IVT is always engaged, even during its zero output adjustment.
IVTs can in some implementations offer better efficiency in the preferred range of operation when compared to other CVTs because most of the power flows through the planetary gear system and not the controlling CVR. Torque transmission capability can also be increased. Staging power splits is also possible for further increase in efficiency, torque transmission capability and better maintenance of efficiency over a wide gear ratio range.
An example of a true IVT is the Hydristor because the front unit connected to the engine can displace from zero to 27 cubic inches (440 cm3) per revolution forward and zero to −10 cubic inches (−160 cm3) per revolution reverse. The rear unit is capable of zero to 75 cubic inches (1,230 cm3) per revolution. However, whether this design enters production remains to be seen. Another example of a true IVT that has been put into recent production[11] and which continues under commercial development[12] is that of Torotrak.
Ratcheting
The ratcheting CVT is a transmission that relies on static friction and is based on a set of elements that successively become engaged and then disengaged between the driving system and the driven system, often using oscillating or indexing motion in conjunction with one-way clutches or ratchets that rectify and sum only "forward" motion. The transmission ratio is adjusted by changing linkage geometry within the oscillating elements, so that the summed maximum linkage speed is adjusted, even when the average linkage speed remains constant. Power is transferred from input to output only when the clutch or ratchet is engaged, and therefore when it is locked into a static friction mode where the driving & driven rotating surfaces momentarily rotate together without slippage.
These CVTs can transfer substantial torque, because their static friction actually increases relative to torque throughput, so slippage is impossible in properly designed systems. Efficiency is generally high, because most of the dynamic friction is caused by very slight transitional clutch speed changes. The drawback to ratcheting CVTs is vibration caused by the successive transition in speed required to accelerate the element, which must supplant the previously operating and decelerating, power transmitting element.
Ratcheting CVTs are distinguished from VDPs and roller-based CVTs by being static friction-based devices, as opposed to being dynamic friction-based devices that waste significant energy through slippage of twisting surfaces. An example of a ratcheting CVT is one prototyped as a bicycle transmission protected under U.S. Patent 5,516,132 in which strong pedalling torque causes this mechanism to react against the spring, moving the ring gear/chainwheel assembly toward a concentric, lower gear position. When the pedaling torque relaxes to lower levels, the transmission self-adjusts toward higher gears, accompanied by an increase in transmission vibration.
Hydrostatic


Hydrostatic transmissions use a variable displacement pump and a hydraulic motor. All power is transmitted by hydraulic fluid. These types can generally transmit more torque, but can be sensitive to contamination. Some designs are also very expensive. However, they have the advantage that the hydraulic motor can be mounted directly to the wheel hub, allowing a more flexible suspension system and eliminating efficiency losses from friction in the drive shaft and differential components. This type of transmission is relatively easy to use because all forward and reverse speeds can be accessed using a single lever.
An integrated hydrostatic transaxle (IHT) uses a single housing for both hydraulic elements and gear-reducing elements. This type of transmission has been effectively applied to a variety of inexpensive and expensive versions of ridden lawn mowers and garden tractors.
One class of riding lawn mower that has recently gained in popularity with consumers is zero turning radius mowers. These mowers have traditionally been powered with wheel hub mounted hydraulic motors driven by continuously variable pumps, but this design is relatively expensive.
Some heavy equipment may also be propelled by a hydrostatic transmission; e.g. agricultural machinery including foragers, combines, and some tractors. A variety of heavy earth-moving equipment, e.g. compact and small wheel loaders, track type loaders and crawler tractors, skid-steered loaders and asphalt compactors use hydrostatic transmission. Hydrostatic CVTs are usually not used for extended duration high torque applications because of the heat that is generated by the flowing oil, although there are a variety of oil cooler designs to help counter this problem.
The Honda DN-01 motorcycle is the first road-going consumer vehicle with hydrostatic drive that employs a variable displacement axial piston pump with a variable-angle swashplate.
AGCO Corporation has employed a hydrostatic CVT transmission in agricultural equipment. The transmission splits power between hydrostatic and mechanical transfer to the output shaft via a planetary gear in the forward direction of travel. In reverse the power transfer is fully hydrostatic.[13]
Naudic incremental (iCVT)
This is a chain-driven system which is advertised at * Although an iCVT works, it has the following weakness:
High frictional losses
The variator pulley of an iCVT is choked using two small choking pulleys. Here one choking pulley is positioned on the tense side of the chain of the iCVT. Hence there is a considerable load on that choking pulley, the magnitude of which is proportional to the tension in its chain. Each choking pulley is pulled up by two chain segments, one chain segment to the left and one to the right of the choking pulley; here if the two chain segments are parallel to each other, then the load on the choking pulley is twice the tension in the chain. But since the two chain segments are most likely not parallel to each other during operations of an iCVT, it is estimated that the load on a choking pulley is between 1 and 1.8 times of the tension of its chain.
Also, a choking pulley is very small so that its moment arm is very small. A larger moment arm reduces the force needed to rotate a pulley. For example, using a long wrench, which has a large moment arm, to open a nut requires less force than using a short wrench, which has a small moment arm. Assuming that the diameter of a choking pulley is twice the diameter of its shaft, which is a generous estimate, then the frictional resistance force at the outer diameter of a choking pulley is half the frictional resistance force at the shaft of a choking pulley.
Shock and durability
The transmission ratio of an iCVT has to be changed one increment within less than one full rotation of its variator pulley. This means that the transmission diameter of the variator pulley, made generally from rubber, has to be changed from a diameter that has a circumferential length that is equal to an integer number of teeth to another diameter that has a circumferential length that is equal to an integer number of teeth; such as changing the transmission diameter of the variator pulley from a diameter that has a circumferential length of 7 teeth to a diameter that has a circumferential length of 8 teeth for example. This is because if the transmission diameter of the variator pulley does not have a circumferential length that is equal to an integer number of teeth, such as a circumferential length of 7½ teeth for example, improper engagement between the teeth of the variator pulley and its chain will occur. For example, imagine having a bicycle pulley with 7½ teeth; here improper engagement between the bicycle pulley and its chain will occur when the tooth behind the ½ tooth space is about to engage with its chain, since it is positioned a distance of ½ tooth too late relative to its chain.
Regarding the previous paragraph, the chain of an iCVT forms an open loop on its variator pulley that partially covers its variator pulley such that an open section, which is not covered by the chain, exist. This is similar to a sprocket of a bicycle where there is a section of the sprocket that is covered by its chain, and a section of the sprocket that is not covered by its chain. During one complete rotation, the toothed section of the variator pulley of an iCVT passes by the open section and re-engages with the chain. Here if the transmission diameter of the variator pulley does not represent an integer number of teeth, improper re-engagement between the teeth of the variator pulley and its chain will occur. Also, the transmission diameter of the variator pulley cannot be changed while the toothed section of the variator pulley is covering the entire open section of its chain loop. Since this is similar to where a plate is glued across the open section of a chain loop, which does not allow expansion or contraction of the chain loop as required for transmission diameter change of the variator pulley. Therefore, the transmission diameter of the variator pulley has to be changed one increment during an interval where the variator pulley rotates from an initial position where a portion of the toothed section of the variator pulley is positioned at the open section of the chain loop but not covering the entire open section, to the final position where the toothed section of the variator pulley passes by the open section of the chain loop and is about to re-engage with the chain. Since it takes less than one full rotation to rotate the variator pulley from its initial position to its final position mentioned in the previous sentence, the transmission diameter of the variator pulley has to be changed one increment within less than one full rotation.
In addition, as the transmission diameter is increased, the chain has to be pushed up the inclined surfaces of the pulley halves of the variator pulley, while the tension in the chain tends to pull the chain towards the opposite direction. Hence a large force, which is larger than the tension in the chain, is required to change the transmission diameter. Since the transmission ratio has to be changed within less than one full rotation of the variator pulley, a large force has to be applied on the pulley halves within a very short duration. If for example the variator pulley rotates at 3600 rpm, which is equivalent to 60 revolutions per second, then the force required to change the transmission ratio has to be applied within 1/60 seconds. This would be similar to hitting something with a hammer. Therefore, here significant shock loads are applied to the variator pulley during transmission ratio change that increases the transmission diameter. These shock loads may cause comfort problems for the driver of the vehicle using an iCVT. Also an iCVT has to be designed as to be able to resist these shock loads which would most likely increases the cost and weight of an iCVT.
Torque transfer ability and reliability
The teeth of the variator pulley of an iCVT are formed by pins that extend from one pulley half to the other pulley half and slide in the grooves of the pulley halves of the variator pulley. Here torque from the chain is transferred to the pins and then from the pins to the pulley halves. Since the pins are round and the grooves are curved, line contact between the pins and the grooves are used to transfer force from the pins to the grooves. The amount of force that can be transmitted between two parts depend on the contact area of the two parts. Since the contact areas between the pins and their grooves are very small, the amount of force that can be transmitted between them, and hence also the torque capacity of an iCVT, is limited.
Another possible problem with an iCVT is that the pins of the variator pulley can fall-out when they are not engaged with their chain, and wear of the pins and the grooves of the pulley halves can cause some serious performance and reliability problems.
Cone


A cone CVT varies the effective gear ratio using one or more conical rollers. The simplest type of cone CVT, the single-cone version, uses a wheel that moves along the slope of the cone, creating the variation between the narrow and wide diameters of the cone.
The more-sophisticated twin cone mesh system is also a type of cone CVT.[14][15]
In a CVT with oscillating cones, the torque is transmitted via friction from a variable number of cones (according to the torque to be transmitted) to a central, barrel-shaped hub. The side surface of the hub is convex with a specific radius of curvature which is smaller than the concavity radius of the cones. In this way, there will be only one (theoretical) contact point between each cone and the hub at any time.
A new CVT using this technology, the Warko, was presented in Berlin during the 6th International CTI Symposium of Innovative Automotive Transmissions, on 3–7 December 2007.
A particular characteristic of the Warko is the absence of a clutch: the engine is always connected to the wheels, and the rear drive is obtained by means of an epicyclic system in output.[16] This system, named “power split”,[17] allows the engine to have a "neutral gear": when the engine turns (connected to the sun gear of the epicyclic system), the variator (i.e., the planetary gears) will compensate for the engine rotation, so the outer ring gear (which provides output) remains stationary.
Radial roller
The working principle of this CVT is similar to that of conventional oil pumps, but, instead of pumping oil, common steel rollers are compressed.[18]
The motion transmission between rollers and rotors is assisted by an adapted traction fluid, which ensures the proper friction between the surfaces and slows down wearing thereof. Unlike other systems, the radial rollers do not show a tangential speed variation (delta) along the contact lines on the rotors. From this, a greater mechanical efficiency and working life are claimed.[19]
Planetary
_in_planet_configuration.jpg)
In a planetary CVT, the gear ratio is shifted by tilting the axes of spheres in a continuous fashion, to provide different contact radii, which in turn drive input and output discs. The system can have multiple "planets" to transfer torque through multiple fluid patches. One commercial implementation is the NuVinci Continuously Variable Transmission.
History
Leonardo da Vinci, in 1490, conceptualized a stepless continuously variable transmission. Milton Reeves invented a variable-speed transmission for saw milling in 1879, which he applied to his first car in 1896.[21] The first patent for a friction-based belt CVT for a car was filed in Europe by Daimler and Benz in 1886, and a US patent for a toroidal CVT was granted in 1935.[22][23]
In 1910, Zenith Motorcycles built a V-twin engined motorcycle with the Gradua-Gear, which was a CVT. In 1912, the British motorcycle manufacturer Rudge-Whitworth built the Rudge Multigear. The Multi was a much improved version of Zenith’s Gradua-Gear.
An early application of CVT was in the British Clyno car, introduced in 1923.
In 1926, George Constantinesco produced the Constantinesco car with a smooth, efficient, inertial masses CVT, which he had invented in 1923, built into the two-cylinder engine.
A CVT, called Variomatic, was designed and built by Hub van Doorne, co-founder of Van Doorne's Automobiel Fabriek (DAF), in the late 1950s, specifically to produce an automatic transmission for a small, affordable car. The first DAF car using van Doorne's CVT, the DAF 600, was produced in 1958.[24] Van Doorne's patents were later transferred to a company called VDT (Van Doorne Transmissie B.V.) when the passenger car division was sold to Volvo in 1975; its CVT was used in the Volvo 340. In 1995, VDT was acquired by Robert Bosch GmbH.
For the 1965 model year, Wheel Horse Products, Inc., of South Bend, Indiana, USA, introduced the first garden tractors equipped with an hydraulic CVT. The models 875 and 1075 included an Eaton-manufactured variable-displacement swash-plate pump and fixed-displacement gear-type hydraulic motor combined into a single compact package, which attached directly to the patented Wheel Horse Unidrive™ transaxle. Reverse was produced by reversing the flow of the pump through over-centering of the swash plate. Acceleration was limited and smoothed through use of pressure accumulator and relief valves located between the pump and motor, to prevent the sudden changes in speed possible with a direct hydraulic coupling. Subsequent versions included fixed swash plate motors, and ball pumps and were sourced from both Eaton and Sundstrand Corp.
Many snowmobiles use a rubber belt CVT. In 1974, Rokon offered a motorcycle with a rubber belt CVT.
CVTs are used in some all terrain vehicles. The first ATV equipped with CVT was Polaris's Trail Boss in 1985.
In February 1987, Subaru launched the Justy in Tokyo with an electronically controlled continuously variable transmission (ECVT) developed by Fuji Heavy Industries which owns Subaru, and Van Doorne's Transmissie in The Netherlands. One and a half years later in November 1988, Subaru also brought out the Justy 4WD ECVT, a Justy with part-time 4WD and the ECVT gearbox. Production was limited to 500 units per month as Van Doorne's could only produce this many steel belts for them. In June, supplies increased to 3,000 per month and Subaru responded by installing the extra volume into transmissions for their Rex microcar.[25] In 1989 the Justy became the first production car in the U.S. to offer CVT technology. While the Justy saw only limited success, Subaru continues to use CVT in its kei cars to this day, while also supplying it to other manufacturers.[26] Subaru offers CVT (Lineartronic) on 2014 Outback, Legacy, Forester, Impreza, and Crosstrek.[27]
In summer 1987, the Ford Fiesta and Fiat Uno became the first mainstream European cars to be equipped with steel-belted CVT (as opposed to the less robust rubber-belted DAF design). This CVT, the Ford CTX was developed by Ford, Van Doorne, and Fiat, with work on the transmission starting in 1976.[26]
The 1992 Nissan March contained Nissan's N-CVT based on the Fuji Heavy Industries ECVT.[26] In the late 1990s, Nissan designed its own CVT that allowed for higher torque and included a torque converter. This gearbox was used in a number of Japanese-market models. Nissan is also the only car maker to bring a roller-based CVT to the market in recent years. Their toroidal CVT, named the Extroid, was available in the Japanese market Y34 Nissan Gloria and V35 Skyline GT-8. However, the gearbox was not carried over when the Cedric/Gloria was replaced by the Nissan Fuga in 2004. The Nissan Murano, introduced in 2003, and the Nissan Rogue, introduced in 2007, also use CVT in their automatic transmission models. In a Nissan press release, dated 12 July 2006, Nissan announced a large-scale shift to CVT transmissions when they selected their XTronic CVT technology[28] for all automatic versions of the Versa, Cube, Sentra, Altima and Maxima vehicles in North America, making the CVT a mainstream transmission system. One major motivator for Nissan to make a switch to CVTs was as a part of their 'Green Program 2010' aimed at reducing CO2 emissions by 2010. The CVT found in Nissan’s Maxima, Murano and the V6 version of the Altima is considered to be the world's first "3.5 L class" belt CVT and can hold much higher torque loads than other belt CVTs.[29]
After studying pulley-based CVT for years, Honda[30] also introduced their own version on the 1995 Honda Civic VTi. Dubbed Honda Multi Matic, this CVT gearbox accepted higher torque than traditional pulley CVTs, and also includes a torque converter for "creep" action. The CVT is employed in the Honda City ZX that is manufactured in India and Honda City Vario manufactured in Pakistan.
In 1996, Fendt, a Germany-based tractor manufacturer, released the first ever heavy-duty tractor to be equipped with a hydrostatic type CVT with the Fendt Vario 926.[31] A year later Fendt was acquired by AGCO Corporation which expanded the use of the transmission to the Challenger Tractor, Massey Ferguson, and TerraGator[32] brands of machinery, which are also owned by AGCO. Well over 100,000 agricultural tractors have been manufactured with this transmission design.[31]
Toyota used a Power Split Transmission (PST) in the 1997 Prius, and all subsequent Toyota and Lexus hybrids sold internationally continue to use the system (marketed under the Hybrid Synergy Drive name). The HSD is also referred to as an electronically controlled continuously variable transmission. The PST allows either the electric motor or the internal combustion engine (ICE) or both to propel the vehicle. In ICE-only mode, part of the engine's power is mechanically coupled to the drivetrain, with the other part going through a generator and a motor. The amount of power being channeled through the electrical path determine the effective gear ratio. Toyota also offers a non-hybrid CVT called Multidrive for models such as Avensis.
Audi has, since 2000, offered a chain-type CVT (multitronic) as an option on some of its larger-engine models, for example the A4 3.0 L V6.
Fiat in 2000 offered a Cone-type CVT as an option on its hit model Fiat Punto (16v 80 PS ELX,Sporting) and Lancia Y (1.2 16V).
BMW used a belt-drive CVT (manufactured by ZF Friedrichshafen) as an option for the low- and middle-range MINI in 2001, forsaking it only on the supercharged version of the car where the increased torque levels demanded a conventional automatic gearbox. The CVT could also be manually "shifted" if desired with software-simulated shift points.
MG-Rover used an identical ZF CVT transmission on its Rover 45 and MG ZS models.
GM introduced its version of CVT known as VTi in 2002. It was used in the Saturn Vue and Saturn Ion models.
In 2002 the Suzuki Burgman 650 was the largest-displacement scooter in the world, and first two-wheel vehicle to feature an electrically controlled CVT.[33][34]
Mercedes-Benz introduced their version of the CVT Transmission, known as "Autotronic" back in 2004 for the 2005 model year A-Class. And later in 2005 for the 2006 model year B-Class. "Autotronic" is one of the most compact CVT Transmissions in the world.
Ford introduced a chain-driven CVT known as the CFT30 in their 2005 Ford Freestyle, Ford Five Hundred and Mercury Montego. The transmission was designed in cooperation with German automotive supplier ZF Friedrichshafen and was produced in Batavia, Ohio at Batavia Transmissions LLC (a subsidiary of Ford Motor Company) until 22 March 2007. The Batavia plant also produced the belt-driven CFT23 CVT which went in the Ford Focus C-MAX, which didn't have much success because of gearbox failures, as it was coupled to the 1.6 TDCi turbodiesel engine, which had a higher torque rating than the CVT can handle. Ford also sold Escort and Orion models in Europe with CVTs in the 1980s and 1990s.
Contract agreements were established in 2005 between MTD Products and Torotrak for the first full toroidal system to be manufactured for outdoor power equipment such as jet skis, ski-mobiles and ride-on mowers.[35]
The 2007 Dodge Caliber and the related Jeep Compass and Jeep Patriot employ a CVT using a variable pulley system as their optional automatic transmission.[36]
The 2008 Mitsubishi Lancer model is available with CVT transmission as the automatic transmission. DE and ES models receive a standard CVT with Drive and Low gears; the GTS model is equipped with a standard Drive and also a Sportronic mode that allows the driver to use 6 different preset gear ratios (either with the shifter or steering wheel-mounted paddle shifters).
The 2009 SEAT Exeo is available with a CVT automatic transmission (multitronic) as an option for the 2.0 TSI 200 hp (149 kW) petrol engine, with selectable 'six-speeds'.[37]
In 2010, the US Patent Office issued patent number 7,647,768 B1 for a series of hydraulic torque converters that use hydraulic friction rather than mechanical friction as a CVT.
Suzuki has used CVT since 2010 on their SX4 and Kizashi models.
In 2016, FCA US LLC announced the 2017 Chrysler Pacifica Hybrid minivan which uses a CVT instead of the 9-speed automatic found in gasoline versions.[38]
See also
- Constant Speed Drive
- Friction drive
- Kinetic energy recovery system (in motorsport)
- List of automobiles with continuously variable transmissions
- Planetary gear
- Power band
- Variomatic
Notes
- ↑ Harris, William. "Diagram of Pulley-based CVTs". Auto.howstuffworks.com. Retrieved 17 June 2011.
Vigneshraj M - Refer him for Better knowledge
References
- ↑ "cvt efficiency". zeroshift.com. Archived from the original (PDF) on 28 September 2014. Retrieved 22 April 2014.
- ↑ "use of clutch with CVT". Scootnfast.com. Retrieved 6 January 2012.
- ↑ Keith Collantine (3 May 2007). "Banned! Continuously Variable Transmission". F1fanatic.co.uk. Retrieved 17 June 2011.
- ↑ Fischetti, Mark (January 2006). "No More Gears". Scientific American. 294: 92. doi:10.1038/scientificamerican0106-92.
- ↑ "Developments in Full-Toroidal Traction Drive Infinitely & Continuously Variable Transmissions (CTI Innovative Automotive Transmissions Conference and Exhibition)" (PDF). Torotrak. August 2007.
- ↑ "Magnets offer advantages as an alternative to mechanical gears". Engineer Live. 7 February 2012. Retrieved 2012-02-07.
- ↑ Chas. A. Trask, Tractor Friction Transmissions, Journal of the Society of Automotive Engineers, Vol. II, No. 6 (June 1918); page 440. Compare Fig. 2, the Elgin Tractor, with Fig. 12, the Plymouth Locomotive.
- ↑ Jones, Franklin D., et al. (1930). Ingenious Mechanisms for Designers and Inventors. Industrial Press. ISBN 0-8311-1084-8. pp. 343–345, Volume I.
- ↑ "drives". Zero-max.com. Retrieved 19 September 2009.
- ↑ "FEVj Infinitely Variable Transmission". Fuel-efficient-vehicles.org. 2 August 1994. Retrieved 19 September 2009.
- ↑ "Torotrak announces commencement of pilot build at Infinitrak and Infinitrak's first product - the Twin Toroidal Transmission" (PDF). Torotrak. 13 April 2011.
- ↑ "Further commitment by Allison Transmission, Inc" (PDF). Torotrak. 13 April 2011.
- ↑ "AGCO's Continuously Variable Transmission (CVT) Explained". Retrieved 26 October 2012.
- ↑ "CVT Explained". Retrieved 27 August 2011.
- ↑ "CVT transmission". Retrieved 27 August 2011.
- ↑ "Toyota Prius - Power Split Device". Eahart.com. Retrieved 14 December 2010.
- ↑ "John's Stuff - Toyota Prius Education - Power Split Device". John1701a.com. 31 January 2006. Retrieved 14 December 2010.
- ↑ "Radial roller CVT patent". Girottobrevetti.com. Retrieved 2012-03-17.
- ↑ "G-Rotor IVT". Girottobrevetti.com. Retrieved 2012-11-10.
- ↑ Hampl, Jasoň; Vítek (2006). "A New Concept of Infinitely Variable Transmission for Mechanically Powered Gyrobuses". Mecca. 4 (1+2): 18–27.
- ↑ A Tale of Two Brothers, Gas Engine Magazine
- ↑ Harris, William. "How CVTs Work". HowStuffWorks, Inc. Retrieved 3 December 2007.
- ↑ McGarry, Ben. "A Proposed Durnin IVT Transmission - A Review by Dr. Ben McGarry, Principal Engineer at e3k Think" (PDF). Infinitely Variable Transmission. Retrieved 11 August 2010.
- ↑ Hilton Holloway, Martin Buckley (2002). 20th Century Cars. Carlton. ISBN 1-84222-835-8.
- ↑ "Fuji Heavy Industries to increase production of ECVT systems". Nihon Keizai Shimbun. Tokyo: 12. 1987-06-13.
- 1 2 3 Poulton, M.L. (1997). Fuel Efficient Car Technology. Computational Mechanics Publications. p. 69. ISBN 1-85312-447-8.
- ↑ https://www.subaru.com/engineering/transmission.html Archived 26 July 2013 at the Wayback Machine.
- ↑ "Nissan Technological Development Activities Overview: Xtronic Cvt". Nissan-global.com. Retrieved 19 September 2009.
- ↑ "CVT". Jatco
- ↑ "Honda Worldwide - Technology Picture Book - CVT". honda.com. Retrieved 19 October 2015.
- 1 2 "Fendt History". Retrieved 26 October 2012.
- ↑ "TerraGator Features". Retrieved 26 October 2012.
- ↑ "Suzuki Electrically-controlled Continuously Variable Transmission (SECVT)". Global Communications Magazine. Suzuki Motor Corp. 1. 2002. Retrieved 18 October 2013.
'Unlike the conventional centrifugal CVT using a rubber belt, the SECVT adjusts the CVT ratio by varying the drive-pulley diameter with an electric actuator motor,' relates Kazutoshi Ohashi who led development of the SECVT control systems in Group I, Miyakoda R&D Centre. 'The SECVT controller calculates the target engine revolution based on the vehicle speed and throttle position, and automatically adjusts the CVT ratio. Unlike conventional systems that adjust the CVT ratio only to the engine revolution, the SECVT's calculation is made with the throttle position — the rider's acceleration choice — also taken into consideration. That optimizes the CVT ratio for actual riding conditions.'
- ↑ Ash, Kevin (29 June 2002). "Press here for 'power' mode". The Telegraph. Retrieved 18 October 2013.
Meanwhile, with a computer to control the transmission ratio, the possibility for gimmicks and gadgets is opened wide - something Suzuki has embraced with open arms. As well as the normal operating mode, a handlebar switch changes the system to 'power' mode, which lets the engine rev some 1,500rpm higher at any given road speed, the intention being to increase power and torque for sharper performance at the expense of economy. But it's the third option that has been fascinating motorcyclists as much as scooter riders - push another button and you switch to manual operation, giving the Burgman a Porsche Tiptronic-style set of button-operated 'gears' to play with.
- ↑ "Torotrak announces agreement to form Joint Venture for high-volume manufacture of IVT technology" (PDF). Torotrak.
- ↑ "Dodge Caliber, Jeep Compass, & Jeep Patriot". The Ecology Center. Archived from the original on 10 March 2008. Retrieved 4 December 2007.
- ↑ "SEAT Exeo 2.0 TSI technical information". Retrieved 14 September 2009.
- ↑ "2017 Chrysler Pacifica: New Look, New Name, New Hybrid Powertrain". Automobile Magazine. Archived from the original on 13 January 2016. Retrieved 11 January 2016.
If buyers do plug in and regularly top-up the battery pack, that number is expected to be 80 mpge, with about 30 miles of all-electric driving possible. Instead of the nine-speed automatic, an electrically controlled continuously variable transmission of Chrysler's own design will divvy up power to the front wheels.